Coater's workflow: Coat the substrate, such as paper, cloth, leather, aluminum foil, plastic film, etc., with a layer of special-purpose glue, paint, or ink, and dry it and rewind it.
The working principle of the automatic coating machine of the coating machine: The working principle of the automatic coating machine for screen printing plate making is the same, but its performance varies according to different models and different manufacturers. The screen coating machine is provided with a device capable of clamping a frame in a vertical rack. The front and back of the screen area is a horizontal coating mechanism. The coating mechanism consists of a coating tank, and mechanical or pneumatic components that control the angle and pressure of the coating tank.
Both ends of the coating mechanism are mounted on the vertical support arm of the coating machine, and the coating mechanism is moved up and down along the surface of the screen through the transmission of a belt, a chain or a cable. The transmission mechanism is connected to a servo or variable frequency motor to make it operate smoothly and accurately control the position of the coating mechanism.
Prior to coating, a clean, stretch-absorbing screen is loaded from the front of the coater, and some models can also be loaded into the screen from the side. In models designed for large format frames, side loading is more common, because the frame is large and bulky, and the side loading makes it possible to increase the amount of lifting and handling. When the automatic screen coating machine is operated online with other automatic screen processing equipment (such as cleaning equipment, regenerating equipment, drying equipment and developing machine), loading from the side is more convenient.
Regardless of how the screen is installed, once the screen is in the correct position, the pneumatic clamping device or the mechanical clamping device is closed, locking the screen. In order to facilitate the operation, many models have a foot pedal to control the clip action, and the operator can free his hands to control the screen. After the screen is installed, apply the corresponding emulsion to the automatic coating machine and start the coating. According to the functions of the control system and the equipment, the equipment can coat both sides of the screen at the same time.
There are two kinds of coating methods. One is to coat the sensitized emulsion on the screen through multiple wet-pressing operations; or to add a drying process after each coating. A machine that quantitatively coats a liquid (or melt) polymer material such as an adhesive or paint on the surface of a material.
Suitable for the production of flexible substrates such as PVC/PE film
Simply put the glue on the film. Specific controls include gluing, drying, rewinding, and tensioning.
The film can be PVC, PE, PET... It can also be some paper, such as hot melt adhesive on release paper.
The coating machine is designed to meet the packaging requirements for storage, transportation, and mechanized loading and unloading operations of the containerized containers, and has designed and manufactured tray-type coating machines, pressure-top resistance type pull-type coating machines, and pre-pull type automatic film coating machines. Extensive use of export costs, food and beverage, irrigation and irrigation, papermaking, dyes, plastic chemicals, glass ceramics, electromechanical castings, and other product assembly costs, improve production efficiency, but also to prevent the damage of goods in the handling process, and play a role in dust prevention , moisture and cleaning effect.
The working principle of the coating machine is to place the wound object in the center of the turntable, start the rotation of the turntable motor, and naturally drive the rotation of the turntable so that the object can realize the peripheral winding machine. At the same time, the elevator motor is started to drive the entire assembly of the winding and binding machine up and down to achieve the winding of the object in the height direction, which realizes the entire appearance of the object. This not only facilitates the packaging requirements for cargo storage, transportation, and mechanized loading and unloading operations, but also prevents the damage of the goods in the handling process, and acts as a dust-proof, moisture-proof, and cleaner, and also reduces the production cost and improves the production efficiency. In the winding process, the main thing is to adjust the film tension and pass through the film. Generally, the degree of film tension can be achieved by adjusting the rotation speed of the turntable and adjusting the rotation speed of the motor. As long as you know that the faster the speed of the turntable, the slower the motor rotates, the tighter the membrane will be, and the looser the principle will be.
The use of coating machine:
Applicable to shoe materials, electronics industry, sponge, EVA, PE, cloth, etc.
The working principle of the automatic coating machine of the coating machine: The working principle of the automatic coating machine for screen printing plate making is the same, but its performance varies according to different models and different manufacturers. The screen coating machine is provided with a device capable of clamping a frame in a vertical rack. The front and back of the screen area is a horizontal coating mechanism. The coating mechanism consists of a coating tank, and mechanical or pneumatic components that control the angle and pressure of the coating tank.
Both ends of the coating mechanism are mounted on the vertical support arm of the coating machine, and the coating mechanism is moved up and down along the surface of the screen through the transmission of a belt, a chain or a cable. The transmission mechanism is connected to a servo or variable frequency motor to make it operate smoothly and accurately control the position of the coating mechanism.
Prior to coating, a clean, stretch-absorbing screen is loaded from the front of the coater, and some models can also be loaded into the screen from the side. In models designed for large format frames, side loading is more common, because the frame is large and bulky, and the side loading makes it possible to increase the amount of lifting and handling. When the automatic screen coating machine is operated online with other automatic screen processing equipment (such as cleaning equipment, regenerating equipment, drying equipment and developing machine), loading from the side is more convenient.
Regardless of how the screen is installed, once the screen is in the correct position, the pneumatic clamping device or the mechanical clamping device is closed, locking the screen. In order to facilitate the operation, many models have a foot pedal to control the clip action, and the operator can free his hands to control the screen. After the screen is installed, apply the corresponding emulsion to the automatic coating machine and start the coating. According to the functions of the control system and the equipment, the equipment can coat both sides of the screen at the same time.
There are two kinds of coating methods. One is to coat the sensitized emulsion on the screen through multiple wet-pressing operations; or to add a drying process after each coating. A machine that quantitatively coats a liquid (or melt) polymer material such as an adhesive or paint on the surface of a material.
Suitable for the production of flexible substrates such as PVC/PE film
Simply put the glue on the film. Specific controls include gluing, drying, rewinding, and tensioning.
The film can be PVC, PE, PET... It can also be some paper, such as hot melt adhesive on release paper.
The coating machine is designed to meet the packaging requirements for storage, transportation, and mechanized loading and unloading operations of the containerized containers, and has designed and manufactured tray-type coating machines, pressure-top resistance type pull-type coating machines, and pre-pull type automatic film coating machines. Extensive use of export costs, food and beverage, irrigation and irrigation, papermaking, dyes, plastic chemicals, glass ceramics, electromechanical castings, and other product assembly costs, improve production efficiency, but also to prevent the damage of goods in the handling process, and play a role in dust prevention , moisture and cleaning effect.
The working principle of the coating machine is to place the wound object in the center of the turntable, start the rotation of the turntable motor, and naturally drive the rotation of the turntable so that the object can realize the peripheral winding machine. At the same time, the elevator motor is started to drive the entire assembly of the winding and binding machine up and down to achieve the winding of the object in the height direction, which realizes the entire appearance of the object. This not only facilitates the packaging requirements for cargo storage, transportation, and mechanized loading and unloading operations, but also prevents the damage of the goods in the handling process, and acts as a dust-proof, moisture-proof, and cleaner, and also reduces the production cost and improves the production efficiency. In the winding process, the main thing is to adjust the film tension and pass through the film. Generally, the degree of film tension can be achieved by adjusting the rotation speed of the turntable and adjusting the rotation speed of the motor. As long as you know that the faster the speed of the turntable, the slower the motor rotates, the tighter the membrane will be, and the looser the principle will be.
The use of coating machine:
Applicable to shoe materials, electronics industry, sponge, EVA, PE, cloth, etc.
Certificate |
ISO14001, ISO18000, ISO9001 Certificate,
and GS certificate from TUV Company of Germany.
|
Color | Various, according to your requirements |
Materials |
A. Plastic parts: Imported LLDPE E. Outer cover: Soft Covering PVC
(Different material is available according to your needs)
|
Advantage |
a.Anti-UV
b.Anti-static
c.Security
d.Environmental protection e.Uneasy to lose shape |
Function |
1.Can protect children safe when they playing indoor, and let they enjoy the play freely 2.Suitable for improving Children energy and imagination 3.Helping them grow up happily, cleverly, and healthily |
Age Range | Children |
Apply to | Amusement park, gymnasium, Kindergarten, Preschool, etc. |
Packing | Standard export packing |
Remark |
We can design and produce as your requirements |
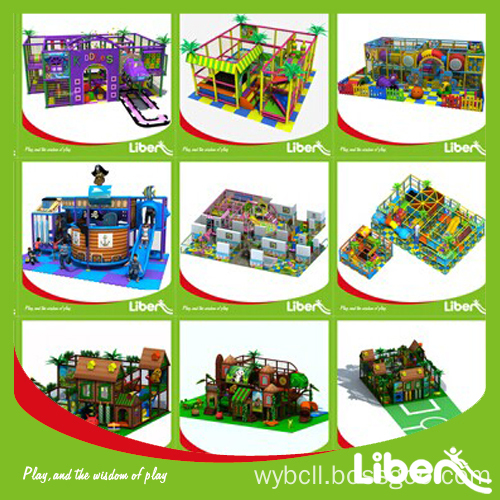
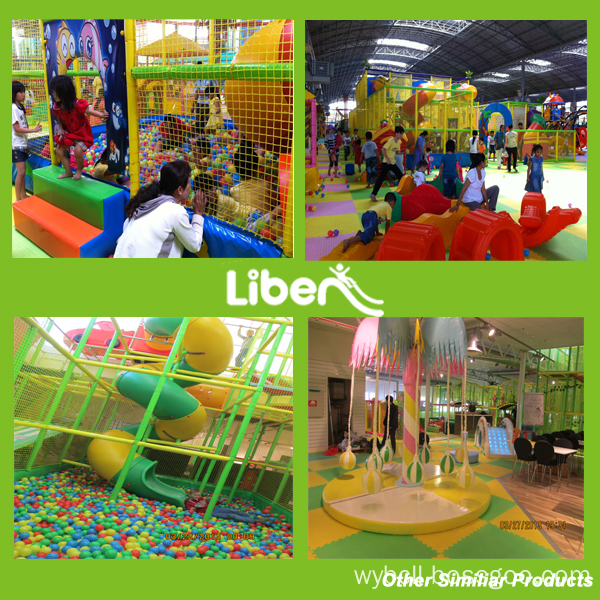
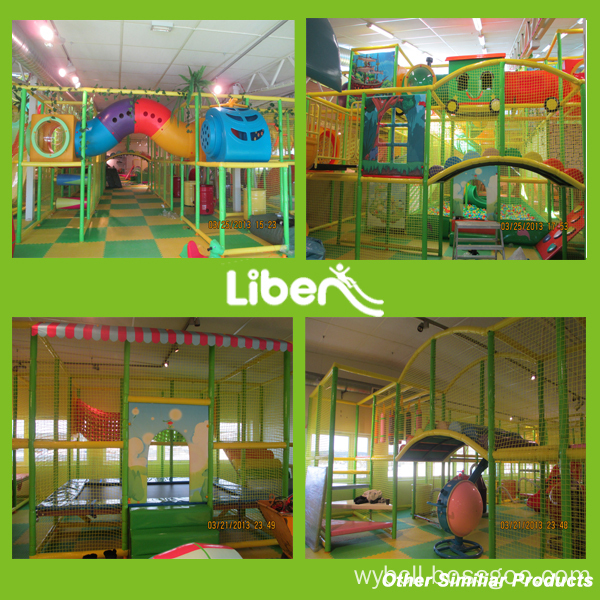
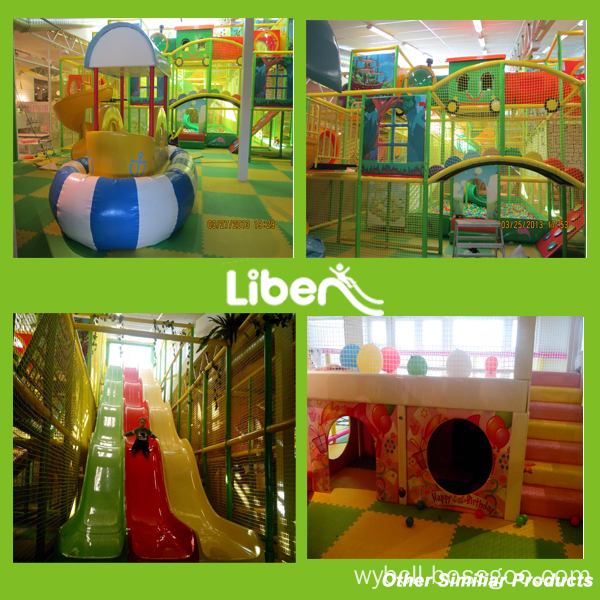
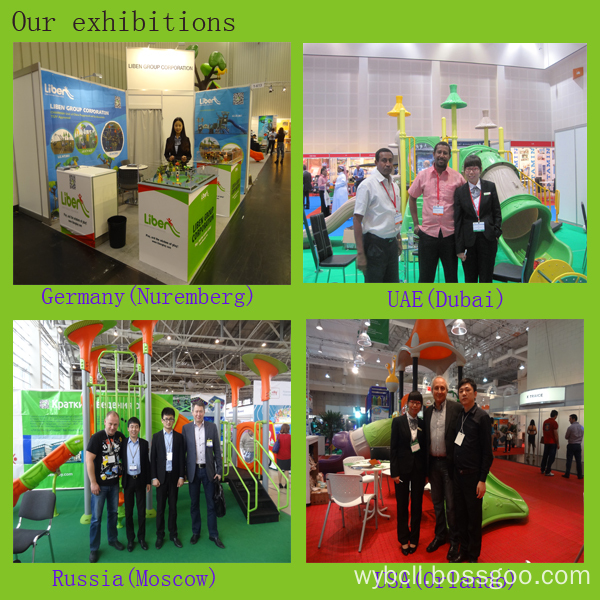
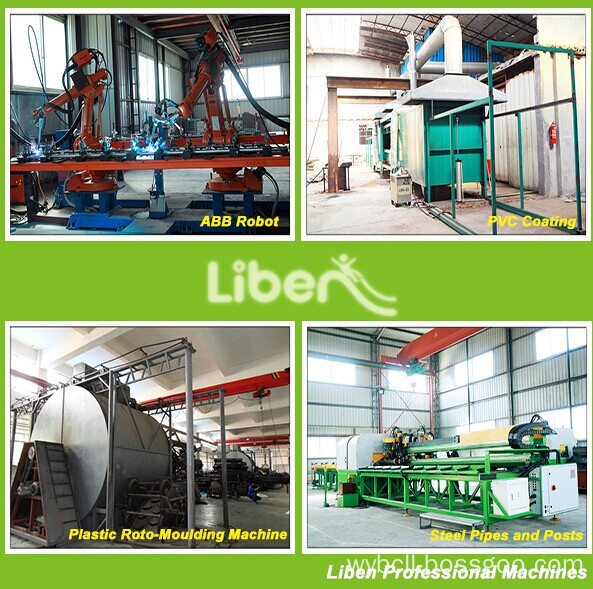
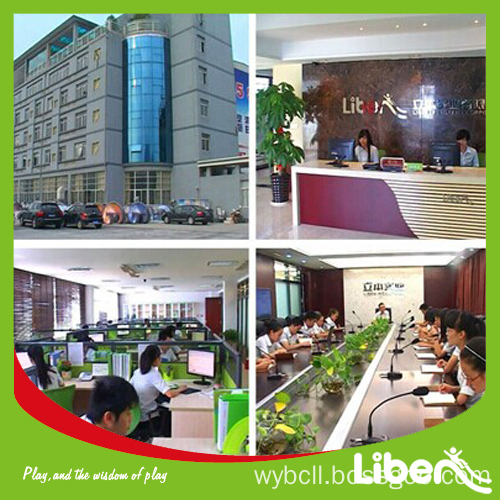
Indoor Electric Playground, Amusement Park Rides, Indoor Electric Rides
Liben Group Corporation , https://www.indoortrampoline.de