Third, gravure printing process elements and control
Printing sequence
Gravure printing usually has two ways of printing and printing. Due to its physical characteristics, paper is basically printed on the surface, and plastic film is used in both ways.
In the process of printing color reproduction, each color version can use its corresponding color ink to superimpose (overprint) to obtain the original color. According to this trapping principle and the actual experience in the production process, the color printing sequence of the general table printing is: white-yellow, magenta-green and black. The printed color sequence in India is: Black, Green and Blue. Spot colors can be placed behind the black, but also behind the three primary colors, and sometimes can be adjusted according to the production schedule.
2. Printing tension control
Printing tension is an important process parameter of the printing process, and its tension system is also the core content of the entire printing equipment. The printing tension is set according to the properties of the substrate. Easy to extend the material is difficult to register, so the tension is generally set to a small, but the tension is too small, the material is loose, irregular movement will occur, nor can it be registered. The tension set value is better than the minimum tension that can be registered and rolled. - The general winding tension is slightly larger than the unwinding tension. The main reason is that the roll is tightened and compacted to avoid loosening and bunching, which is unfavorable to the production of the next compounding and slitting process. The general tension values ​​of easily stretchable BOPP, PE, etc. are set at 100N, and paper, aluminum-aluminum composite materials that are not easily stretched are generally set at about 120N, and NY, PEI, and FM--110N are set at about 110N. For different models and different specifications, the tension setting value will be different.
3. Drying temperature
The control of drying temperature is also determined by the nature of the substrate. There is also a certain relationship between the drying temperature, the printing speed, and the boiling point of the solvent. The temperature is constant, if the boiling point of the solvent is higher, the speed should be reduced, on the contrary, the speed can be high; when the solvent has a constant boiling point, the temperature should be raised appropriately, and vice versa, the temperature can be lowered. When the speed is constant, if the solvent is boiling point, If the temperature is high, the temperature will increase, and vice versa.
In addition, the control of drying temperature is also related to the process conditions, graphic area, ink properties, and ink thickness. White ink, gold ink, silver ink and other temperature requirements are about 10°C higher than normal inks, and full-plate printing ink temperature is generally set at 80°C-90*C (vehicle speed is 150-200m/min).
4. Printing pressure
The printing pressure is the pressure of the printing rubber impression roller. Insufficient printing pressure, poor ink transfer, prone to graphic defects; pressure is too easy to press marks, wrinkles of the film. Therefore, the common gravure printing machine is equipped with electrostatic ink pressure roller, the use of static electricity to help the transfer of ink, it is essential for high-speed gravure. Especially when printing paper, the ink can be transferred to the paper very well by the electrostatic ink-absorbing system. Without an electrostatic ink-absorption system, the ink cannot be fully transferred. Patterns, lines, characters, etc. may appear with flowers, broken lines, and uneven shading and shades. Different substrate printing pressure is different, for example, the surface of rough kraft paper, etc. need a larger printing pressure, about 20-30Pa, printing pressure roller rubber hardness is also higher than the general requirements of plastic film, generally required in 85-90HS. General plastic film pressure is generally around 2Pa. In the specific production process, appropriate adjustments are made according to the effects of the printing layout and the related factors such as the ink.
5. Ink ink level adjustment and control
The accuracy and consistency of ink privacy in the gravure printing process is one of the key points. Especially in high-speed rotary printing, the ink's salary control is related to a series of printing failures and is an important factor influencing the quality of printed products. When printing, the greater the ink hue, the poorer the effect of pigment transfer. When the ink salary is too large, the entire ink system is in an oversaturated state, and pigments and other substances have poor fluidity and are easy to gather together. It is not easy to smoothly enter the publishing network. If the ink's twist is too small, the ink contains many organic solvents, while the resin, pigment, and other components are relatively small, and do not form a smooth film after drying. The ink layer is white, dull, and lacks luster.
When gravure is printed, first adjust the ink's twist, add the solvent to the ink, and reduce its twist to the degree required by the press's performance and conditions. The salary is mainly matched with the printing speed, and the low salary is used when printing at high speed. Since the ink quality greatly affects the printing quality, the ink must be controlled to a suitable degree during the gravure printing process. During the production process, the solvent is constantly evaporating due to non-stop circulation of the ink, and the Tth of the ink should be detected at intervals. If the control exceeds the control range, a new solvent should be added immediately to adjust it to the normal range.
6. Scraper
The use of scraper is a major feature of gravure printing, and it is also one of the important factors that affect the quality of gravure printing. In the printing process, the requirements for the selection, installation and adjustment of the squeegee are very high. Generally, European or Japanese special blades are selected. According to the experience of the actual production process of the worker, the general blade has a contact angle of 55. Ideally, the pressure of the scraper has a great influence on the quality of the printed product. Excessive pressure will reduce the transfer rate of the ink, causing greater wear on the plates and blades. Too small pressure is prone to dirty plates or scraper lines. The degree of abrasion of the doctor blade in different parts of the printing plate is not the same. The abrasion of the doctor blade mainly occurs in the part in contact with the graphic area. Therefore, when different images are printed, especially after a long time of use, the same doctor blade is still used. The knife may not be able to completely scrape the excess ink on the plate roller, and it may also cause streaks and dirty plates.
7. Platen management
Since gravure printing relies mainly on the transfer of ink stored in the gravure cylinder roller pocket to the substrate to achieve the printing pattern, the storage and cleaning of the plate cylinder are particularly important. The place where the printing roller is stored should be kept clean, ventilated, and dry. The printing plate should be carefully cleaned before and after printing to prevent the ink from accumulating in the mesh hole for a long time to block the plate and affect the use. In particular, some fine-stripe plates should be strictly observed. Clean the platen drum before and after printing.
Zhang Xiaohui Yu Guang Province
Print magazine-2006 issue 6
1. Product name:Bevel Cut Egg Shape Puff
2. Size: 60*40mm,38*56mm,40*62mm
3. Shape:Gourd,drop water,olive shapes
4. Certification: SGS.
Product Name
|
Bevel Cut Egg Shape Puff
|
Material
|
Non latex ,hydrophilic sponge
|
Color
|
Pink,black,green,yellow,purple
|
Application
|
makeup tool for foundation
|
Usage
|
cosmetic area for face
|
Feature
|
It will become twice big than original after getting water.
|
Attention
|
don't squeeze hard by hand.
|
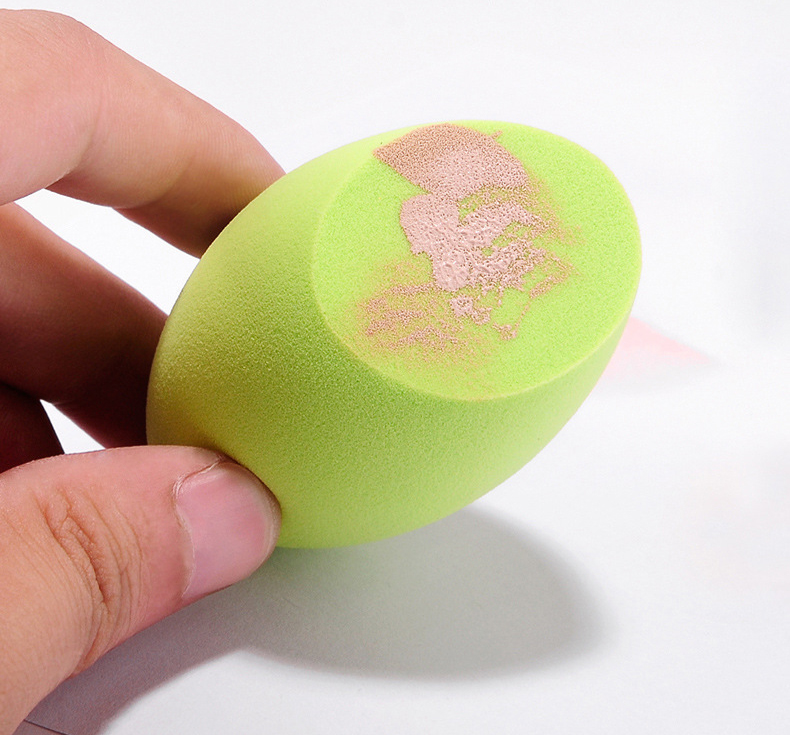
Bevel Cut Egg Shape Puff
Bevel Cut Egg Shape Puff,Bevel Cut Makeup Sponge Puff,Egg Shape Makeup Sponge Puff,Bevel Cut Egg Shape Makeup Sponge
Ji An Chi Cai Gift and Packaging Product Co., Ltd. , http://www.chicaieva.com